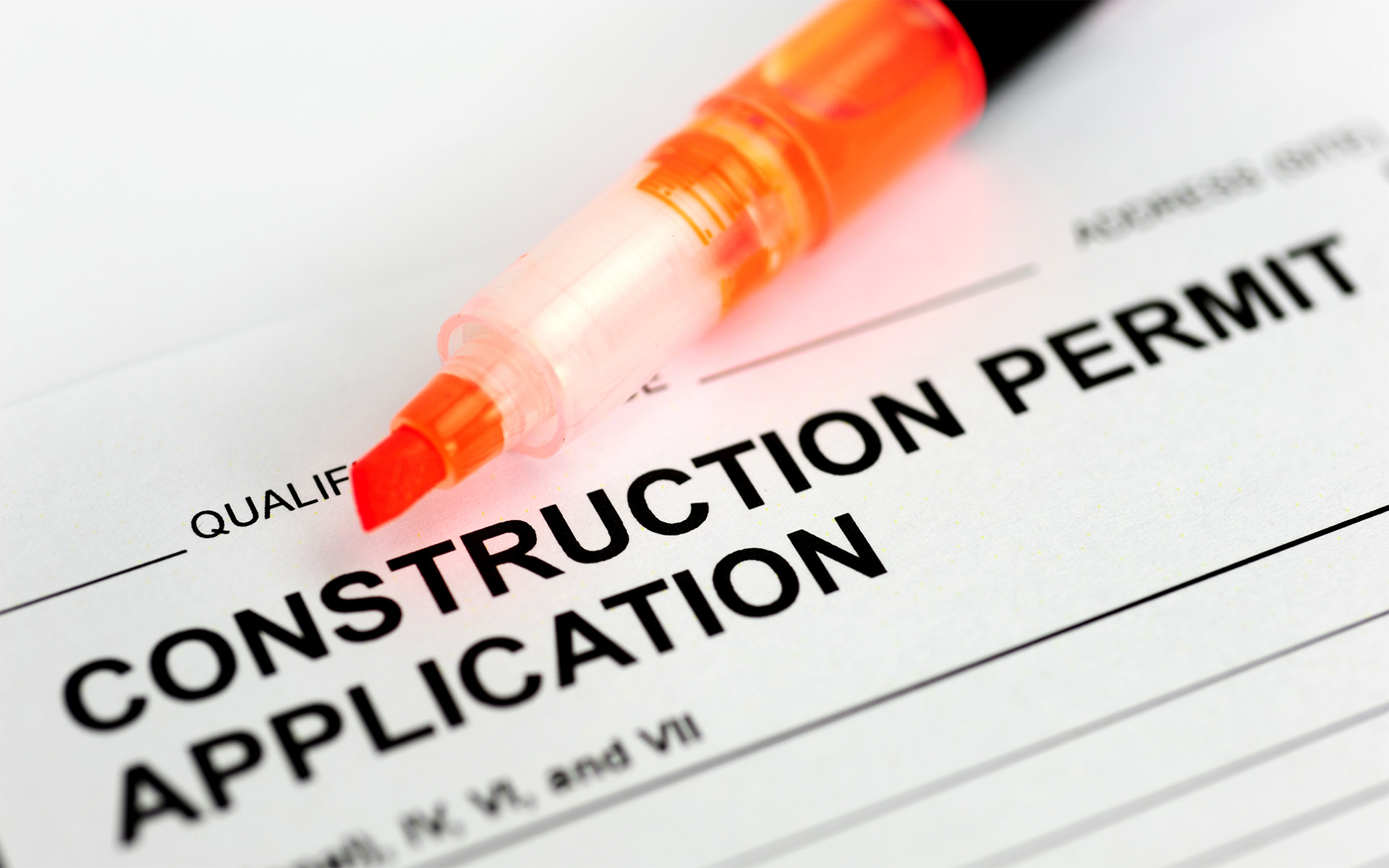
Do I Need A Permit To Install Storage Racks For My Inventory
Signed lease for new warehouse space – what should my next steps be?
- Meet with the general contractor for tenant improvements
- Approve design for offices, office furniture, tile, carpet, paint, etc.
- General contractor applies for permits for electrical / modify fire suppression system / building changes
- Hire a company to install Wi-Fi throughout the building
- Set move-in date
What you’re missing is how do you relocate the inventory and the storage equipment that the inventory sits on……THE PALLET RACK/SHELVING
The pallet racks/shelving/mezzanine/cantilever racks for the new facility require a building permit – PER UBC2018 and most people are unaware of this step and the additional time it takes to be completed and the additional expense involved.
This step should be right up there with the GC/TI meetings………
Definitions
High-Piled Combustible Storage – Storage of combustible materials in closely packed piles or combustible materials on pallets, in racks, or on shelves where the top of storage is greater than 12 feet (3658 mm) in height. Where required by the fire code official, high piled combustible storage also includes certain high-hazard commodities, such as rubber tires, Group A plastics, flammable liquids, idle pallets, and similar commodities, where the top of storage is greater than 6 feet (1829 mm) in height.
High-Piled Storage Area – An area within a building that is designated, intended, proposed, or actually used for high-piled combustible storage, including operating aisles.
Submittal Requirements
If any interior portion of the building is over 500 sq ft and considered “High-Piled Combustible Storage”, the project will be required to submit plans to the Planning and Development Department (PDD) for review. The design shall be in accordance with locally recognized building and fire codes.
- The good news is storage equipment under 5’9” does not require a permit.
- Storage equipment from 5’9” – 12’ is an easier permit to obtain.
- Any storage equipment over 12’ tall will require a floorplan – structural engineering – identify the product being stored – exit doors marked – exit paths indicated, and all documents stamped by a qualified/licensed engineer.
Yes, there are costs involved – the municipalities charge fees, engineers charge fees, and inspections cost money. Plus, there is time involved.
From agreement to floorplan to project costs being approved, a simple permit can take up to 7 weeks to get thru the entire process. Which includes engineer-stamped drawings & structural calculations. This process can typically be taken care of while waiting for the new material to arrive and be installed. If you choose to move your existing material be sure to get the timetable right. We try to get them right every time, but with each municipality, there is always the risk of corrections being required which adds more time so the takeaway should be to have as much time as possible.
Once the permit is approved, the installation can begin. Once complete, there are inspections required: a structural anchor inspection (are the racks anchored properly) completed by an independent, third-party engineering firm and the final inspection by the municipality to verify the installation was according to the engineered, approved plans. Some municipalities also require an inspection from the fire department. This is typically completed after the inventory is loaded on the racks/shelving.
Now the question is how do you accomplish all these steps? You have 2 choices:
You can choose to complete the process on your own. Hire an architect to draft up the plans, find an engineer to stamp your drawings, take multiple trips to city hall, and source an inspector to complete the structural anchor inspection.
OR
You can choose to do business with a material handling company that will take on the entire permit process as a part of the project… Yes, the material handling company does get this accomplished for a fee.
It is your choice, but we are here to help either way.